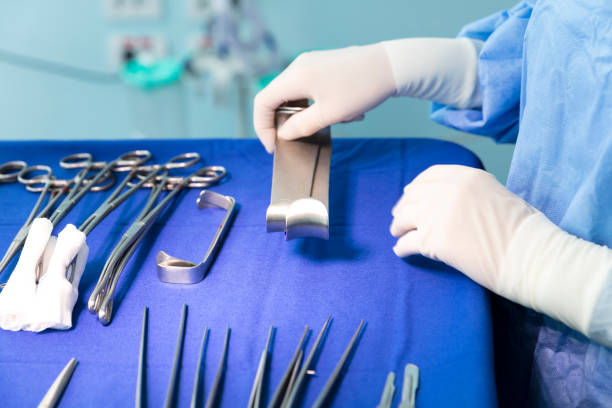
Electropolishing is classified by the Environmental Protection Agency (EPA), as a metal finishing operation in the same category as electroplating. The facility must have proper permits for the generation of waste, maintain proper records of operations, and meet all requirements of Federal, State, and local regulating authorities. To craft materials that follow […]
Electropolishing is classified by the Environmental Protection Agency (EPA), as a metal finishing operation in the same category as electroplating. The facility must have proper permits for the generation of waste, maintain proper records of operations, and meet all requirements of Federal, State, and local regulating authorities.
To craft materials that follow industry standards, the finishing process used on the metal is important to ensuring durability and cleanliness. In the process of electropolishing, burrs and other peaks of surface roughness attract greater electrical current density and erode first in a phenomenon known as anodic leveling. The preferential removal of protruding portions of the surface structure leads to a smoother metal surface.
Common Applications of Electropolishing
Electropolishing has been practiced commercially since the 1930’s. The first widespread use of electropolishing was primarily to add cosmetic appeal to consumer goods such as cookware and fountain pens. In recent years, it’s a common finishing procedure across a wide variety of industries, including the following:
Surgeons and dentists use electropolishing to keep their tools clean.
Food, beverage, and pharmaceutical processors benefit from the sterilizing features of electropolishing.
Appliance manufacturers use electropolishing in appliances like washing machines, microwaves, stoves, and refrigerators to make parts last longer.
Aerospace manufacturers use electropolishing on flight-critical parts to reduce friction and ensure top performance.
Semiconductor manufacturers use electropolishing with fragile, irregularly shaped products.
Automakers and the racing industry electropolish gears and fuel lines to reduce friction, boost performance and ensure long life of parts.
Prepare Parts for Electropolishing
- The first step in the electropolishing process is the cleaning process.
- Prep the metal part by removing larger surface imperfections.
- Ensure metal welds are uniform.
- Remove coatings and adhesives.
For more information, please contact us today at (718) 858-6634.